RaLCシリーズ製品情報/RaLC

RaLC (ラルク)
物流業向けシミュレーションソフトウェア
RaLC は物流センターの倉庫内作業における問題点を見える化するシミュレーションソフトウェアです。また、見えた問題点に対する改善案の改善効果も見える化します。

・倉庫内にモノが溢れている
・予定時刻までに作業が終わらない
・作業員に手待ち時間が発生している

・モノが溢れないために必要な広さは?
・引取人員や作業員の追加は何人必要?
・作業員を省人化できるか?
複数の改善案を事前に比較・検証、それぞれの効果を数値化し、定量的に評価・分析できるため、効率的に改善作業を進めることが可能です。
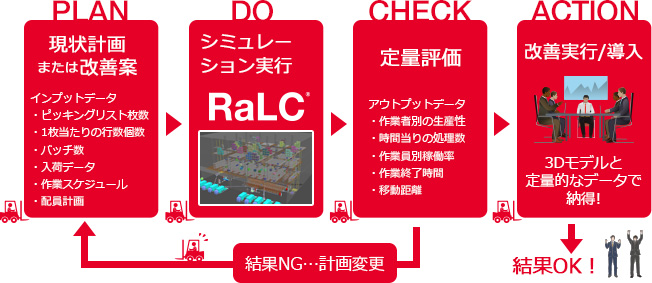
シミュレーションで作業計画の精度アップ
改善案を定量的に評価できれば、顧客/社内/関係者に対する提案の説得力が格段にアップ。さらに3DシミュレーションのRaLCなら、視覚的に納得度の高いプレゼンテーションも可能となります。
RaLCならできる こんな比較

ピッキング方法を比較 | レイアウト/作業員数/ロケーションは同一の条件で、作業方法を「オーダーピッキング」と「トータルピッキング」で変えた場合の生産性を比較した例 |
---|
オーダーピッキング | トータルピッキング | |
---|---|---|
![]() |
![]() |
|
作業時間 | 2時間52分22秒 | 1時間34分42秒 1時間18分40秒削減 |
移動距離 | 28,467.0m/10人 | 19,245.6m/10人 9221.4m削減 |
ピッキング作業 生産性 | 平均 627.82個/h | 平均1,189.95個/h 562.13個/h向上 生産性189%向上 |
レイアウトを比較 | 同一面積でレイアウトを「多階層」と「ワンフロア」で変えた場合の入荷、入庫、ピッキング、仕分け作業の生産性を比較した例 |
---|
平屋の1万坪 | 3F建ての1万坪 | |
---|---|---|
![]() |
![]() |
|
作業時間 | 4時間02分25秒 | 3時間08分34秒 53分41秒削減 |
移動距離 | 251,065.1m | 200,909.3m 50,155.8m削減 |
ピッキングピース数 | 平均 247.7個/h | 平均 320.65個/h 72.95個/h向上 |
ピッキングオーダー数 | 平均 2.48オーダー/h | 平均 8.49オーダー/h 6.01オーダー/h向上 |
ロケーション配置を比較 | 現行ロケーション案と出荷頻度を考慮した新ロケーション案で、入荷/入庫/ピッキング/仕分け作業の生産性を比較した例 |
---|
現行ロケーション | ロケーション変更後 | |
---|---|---|
![]() |
![]() |
|
ロケ割 | 出荷頻度に関係なく全体的に配置 | 出荷頻度が高い品目を手前に配置 (出荷頻度:1列目A品/2列目B品15%、3列目C品5%) |
作業時間 | 2時間00分09秒 | 1時間43分23秒 16分46秒削減 |
移動距離 | 10.05Km/4人 | 8.15Km/4人 1.9Km削減 |
ピッキング作業生産性 | 平均 282.67個/h | 平均 290.45個/h 7.88個/h向上 |
シミュレーションから見える問題点
これまで感覚的にしか分からなかった物流センター内の作業や倉庫レイアウトの問題点。シミュレーションなら様々な角度から見える化可能です。定量的かつ視覚化されたシミュレーション結果から、改善のヒントがきっと見つかります。
RaLCの出力で見える こんな問題点

作業員の稼働率/稼働状況 |
---|
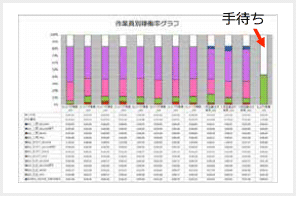
作業員別稼働率グラフ
作業者別/アクティビティ別の稼働率を表示します。白い部分は「手待ち」時間です。
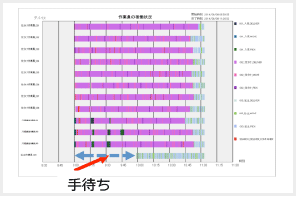
作業員の稼働状況(タイムスタンプグラフ)
作業者別/アクティビティ別の稼働を時間軸に沿って塗り分けます。色塗時間帯は作業中です。色と色の間の白色時間帯は「手待ち」時間です。
グラフから見える問題点の一例
稼働率の低い作業員がいる
低稼働作業を集約し、作業員の多能工化(1人で複数の異なる作業を請負う)によって、省人化できる可能性があります。多能工化の際、従来の設計手法では考慮できない複数作業場所間の「移動時間」を考慮したシミュレーションが可能です。
特定の作業員だけ稼働率が高い
高稼働の作業員が全体の能力を決める=ボトルネックになっている可能性があります。高稼働作業を分散し、全作業員の稼働率を向上させることで処理能力が向上します。
生産性向上に繋がらない作業(移動など)が多い
レイアウト変更、担当業務配分変更、搬送機器の導入などによって処理能力が向上する可能性があります。
色抜け時間帯が多い作業員がいる
手待ち時間が多い作業員がいます。午前のみ、午後のみなど業務シフトの変更で省人化できる可能性があります。
移動距離 |
---|
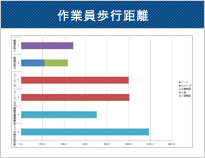
移動距離グラフ
作業者別の移動距離を表示します。
グラフから見える問題点の一例
移動距離が長い
レイアウト改善で移動距離や作業時間を短縮できる可能性があります。
移動距離が短い
作業員が多く、作業員数削減/省人化できる可能性があります。
動線・滞留状況 |
---|
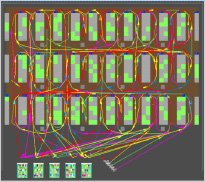
動線グラフ・滞留表示
作業員・フォークリフト・AGVなどの移動体別にシミュレーションモデル内の歩行動線/走行動線を時系列で表示します。
グラフから見える問題点の一例
動線交差が多い場所がある
接触事故などの危険性があります。
通過待ちなどの待ち時間が発生している可能性があります。
出荷頻度が低いエリアへのアクセスが多い
ロケーション変更によって移動距離を削減できる可能性があります。
スループット |
---|
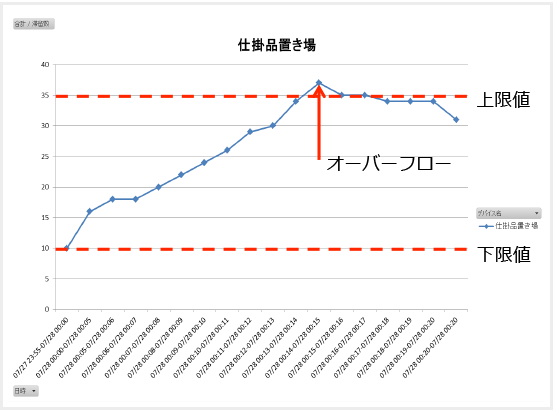
スループットグラフ
各ポイントでの滞留数・流入数・流出数を時系列でグラフ化します。
グラフから見える問題点の一例
積載数が想定上限値を超えている
正しい場所に積載できず、モノが溢れる可能性があります。
積載数が想定下限値を超えている
中間仕掛品置き場の場合、後工程が「材料不足」である可能性があります。
生産性 |
---|
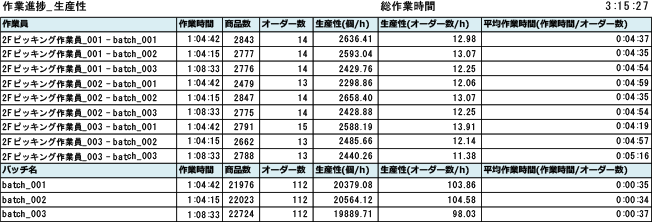
生産性分析グラフ
作業者ごとの生産性(1時間当りの作業実績)を出力します。
グラフから見える問題点の一例
生産性が想定値と異なる
改善のためには、他のグラフを参考に問題点の目星をつけ、レイアウト・ロケーション・配員を変更したシミュレーションを行い、変更後の生産性を再度確認します。
簡単操作でシミュレーション
効率的に改善作業を進めるために、シミュレーションを簡単に行えることが必要です。RaLCには、シミュレーションを素早く行うための様々な工夫が用意されています。
モデル作成方法 |
---|
・作業員はもちろん、各種物流機器(コンベア・フォークリフトなど)は、あらかじめテンプレート(デバイス)として用意されています。
・建屋を構築し、各種デバイスを配置することで、物流現場のイメージを再現できます。
・色・形・速度・大きさなどは各種プロパティに入力することで、設定変更可能です。
・基本的な操作方法はWindowsに準拠しています。
・複数デバイスを組合わせた「ユニット」の作成も可能です。
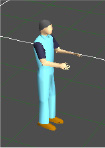
≪作業員≫
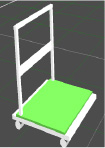
≪台車≫
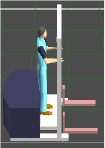
≪フォークリフト≫
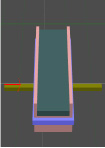
≪AGV≫
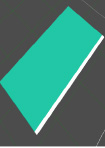
≪仮置き場≫
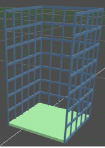
≪カゴ車≫
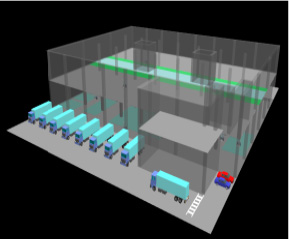
≪建物全体≫
「誰でも・早く・簡単に」使える |
---|
RaLC物流ワークフロー(オプション)で簡単シミュレーション
・作業方法はテンプレート/プルダウンから選択!
・コマンド入力は一切無し!!
・投入データをExcelで作成可能!!!
シミュレーションモデル作成工数40~50%ダウン!!!!
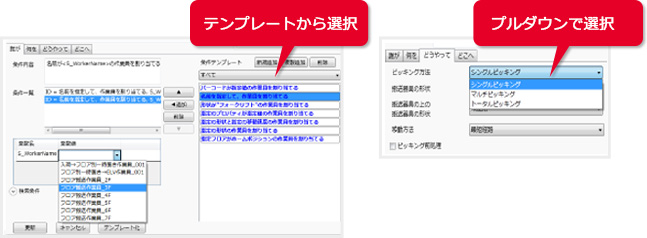
RaLC物流ワークフロー ご利用ユーザー様からのご評価
![]() |
プログラミングの必要がないので、PCの基本操作ができればシミュレーションモデルが作成できる。(大手3PL企業様) |
![]() |
投入データをExcelで作成可能なので、Excelが使えればシミュレーションモデルが作成できる。(大手マテハン企業様) |
![]() |
入荷/検品/ピッキング/仕分けなど物流センター内の一連の作業を物流ワークフローでシミュレーションできる。(多数のユーザー様) |